Seals
Pump Mechanical Seals
The company is a well known Manufacturer, Exporter, Importer, and Supplier of the finest Centrifugal Pump Mechanical Seals. The Centrifugal Pump Mechanical Seal acts as a check valve and a slider bearing. The obvious function of our Centrifugal Pump Mechanical Seals is that of a check valve to prevent liquid under pressure from leaking out of the pump, or from drawing air into the pump when under vacuum conditions.
Description
- Seal Life : Since the seal must function as a slider or friction bearing, the seal has an unpredictable life span. The seal of a centrifugal pump is usually replaced many times during the life of a pump. All bearing need lubricant and the seal lubricant is the liquid being pumped. Liquid infiltrates between the contact faces of the primary and mating rings. Some of this liquid does find its way through to the atmosphere but is so slight as to only be noticed as corrosion of 'build up' on the pump adapter. The condition of the pumped liquid will greatly affect seal life
- Abrasives : The number one enemy of a Centrifugal Pump Mechanical Seals is abrasive particles in the liquid being pumped. Abrasives may be anything from dirt to dissolved impurities in the liquid precipitating out of solution. These abrasive particles infiltrate with the liquid between the seal faces and grind away the carbon primary ring, the normal shiny face of the primary ring and mating ring
- Heat Damage : Excessive heat can damage the seal in two areas - the primary ring and the elastomer parts. The primary ring is made primarily of carbon. The pump should be operated without liquid - even for a very short period - the primary and mating ring faces are denied lubricant. This causes the faces to become very hot. The binder mixed with the carbon breaks down and the face of the primary ring turns to a dull black powder.
The O-ring, or cup, and flexible diaphragm of the seal are made of one of many types of rubber-like substance called an 'elastomer'. The type of elastomertic material is selected to match the temperature limit and types of material being pumped. Should the temperature limit be exceeded, the diaphragm and O-ring will become hard and sometimes crack. The seal will then start to leak. - Conclusion : The forgoing is a brief discussion of some of the most common reason why seal life is shortened. Under normal conditions, seals wear out much faster than the other pump parts. Abrasives and excessive heat greatly shorten the seal's life span
- Brand Offered : Eagle Burgmann
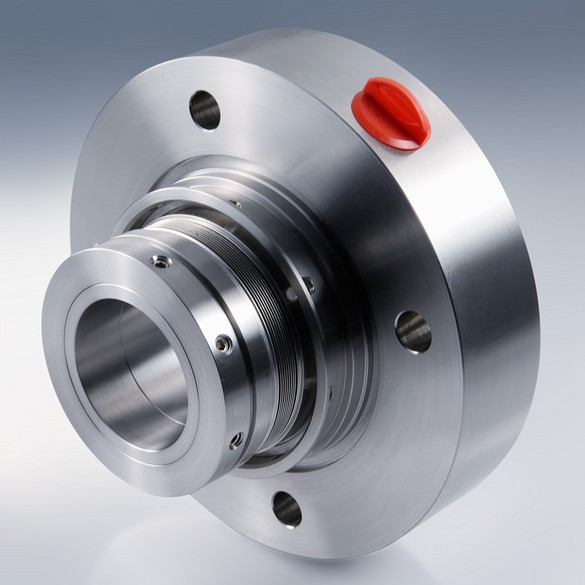
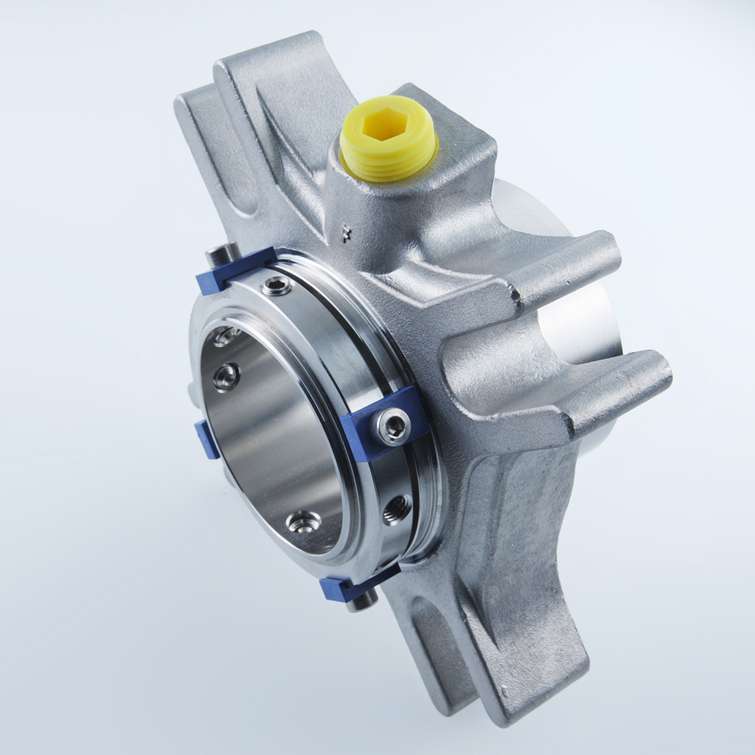
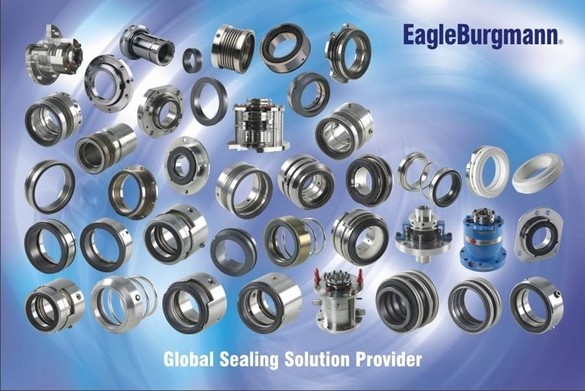
Agitator Seals
The Agitator Seals have been developed to equip vessels with constructional and dimensional parameters according to DIN 28136 and ensure sealing of the mixers rotating shaft to the stationary reactor part.
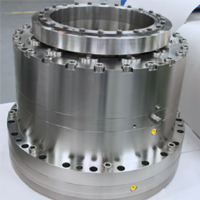
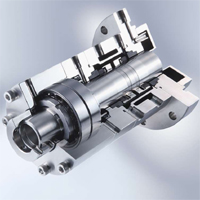
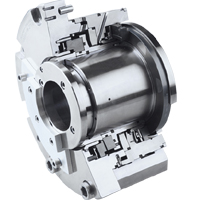
Compressor seal
Compressor process seals are designed to seal the rotating assembly in the stationary compressor case to prevent the process gas in the compressor from getting to the atmosphere and to prevent the atmosphere from getting into the process gas.
